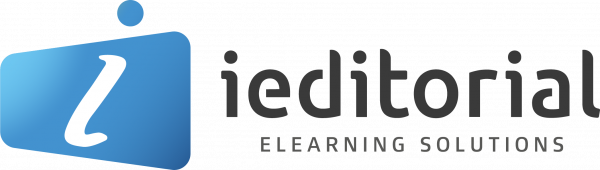
MF0578_3 SISTEMAS DE CONTROL AVANZADO Y DE OPTIMIZACIÓN DE PROCESOS
Información adicional
Horas | 90 |
---|---|
Código | |
Formato | Digital |
Proveedor | IEDITORIAL |
Certificado de profesionalidad |
53,10 €
*Los precios no incluyen el IVA.
Objetivos
Contenidos
Objetivos
– Describir los sistemas de control avanzado, relacionándolos con la producción, rendimiento y calidad del proceso químico.
– Caracterizar el control avanzado de la calidad en procesos químicos industriales y de producción de energía y otros servicios auxiliares.
– Manejar el sistema de control avanzado y las aplicaciones de optimización en procesos químicos industriales y de producción y distribución de energía y otros servicios auxiliares.
– Evaluar el control avanzado y de optimización como elementos fundamentales de la planificación, organización y control de los diferentes procesos químicos y de producción de energía y otros servicios auxiliares.
– Caracterizar el control avanzado de la calidad en procesos químicos industriales y de producción de energía y otros servicios auxiliares.
– Manejar el sistema de control avanzado y las aplicaciones de optimización en procesos químicos industriales y de producción y distribución de energía y otros servicios auxiliares.
– Evaluar el control avanzado y de optimización como elementos fundamentales de la planificación, organización y control de los diferentes procesos químicos y de producción de energía y otros servicios auxiliares.
Contenidos
MÓDULO 1. SISTEMAS DE CONTROL AVANZADO Y DE OPTIMIZACIÓN DE PROCESOS
UNIDAD DIDÁCTICA 1. EL CONTROL “AVANZADO”. DESARROLLOS POSTERIORES AL CONTROL PID.
Variantes del control avanzado.
– Control en cascada. Control anticipativo (feed forward).Control Adaptativo. Control predictivo basado en modelo (MPC). Control óptimo. Control multivariable. DMC (dinamic matriz control).
– Otras estructuras de control: Control por ratio. Control de gama de partida. Control de máximos (override).
UNIDAD DIDÁCTICA 2. CONTROLADORES LÓGICOS PROGRAMABLES (PLC).
Los PLCs: Introducción. Conceptos Básicos. Principios de funcionamiento:
– Representación, convención de símbolos y colores.
– Hardware PLC, Sofware PLC. Principios de lógica y lenguaje de programación.
– Estructura de un PLC: Rack. Bastidor o chasis. Fuente de alimentación. CPU (Sistema operativo y Procesador). Módulos de Entradas (discretas y analógicas). Módulos de Salidas (discretas y analógicas). Memoria. Tiempo de scan.
– Control y programación de procesos utilizando autómatas programables.
* Introducción. Ejemplo ilustrativo.
* Ecuaciones lógicas. Sistemas lógicos combinacionales y secuenciales.
* Aplicación al control de motores. Aplicación a los sistemas de alarma y de seguridad. Aplicación al control de proceso: regeneraciones, arranques, paradas, otras.
UNIDAD DIDÁCTICA 3. SISTEMAS DE CONTROL DIGITAL (SCD, SCADA) EN INDUSTRIA QUÍMICA.
Control Distribuido:
– Definición de Control Distribuido. Descripción general: sistemas analógicos y sistemas digitales.
– Controlador básico (regulador digital). Controlador Multifunción.
– Estación de trabajo del operador.
– Elementos principales: alimentación eléctrica, conexiones de entrada de señal, salidas de señal, módulos e control, módulos de cálculo, registros y
almacenamiento, pantallas de visualización y sistema de operación.
– Secciones y niveles que forman un Control Distribuido.
* Nivel 1 (planta, proceso, sensores, módulos E/S etc.).
* Nivel 2 (control y regulación, controladores, PLCs, PCs etc.).
* Nivel 3 (mando de grupos, PLCs, PCs etc.).
– Nivel 4 (dirección de la producción, estaciones de trabajo, supervisión del
producto, aplicaciones en red).
– Descripción del camino recorrido por la señal de campo (analógica y
digital) hasta la pantalla de trabajo. Indicar con un ejemplo concreto los
elementos por los que circula la señal y los valores que adquiere.
– Descripción del camino recorrido por la señal (orden dada por el operador) desde la pantalla de trabajo hasta el elemento final. Hacer la descripción de forma grafica mediante un ejemplo real.
– Robustez del sistema. Estructuras que la mejoran. Configuraciones del sistema ante el fallo de elementos principales.
– Comunicación del operador con el sistema: El teclado. El ratón. La pantalla táctil.
– Interacción del operador con el sistema. Contenido de las pantallas de trabajo:
* Diagrama de flujo (activo) de la planta en pantalla.
* Indicación en tiempo real de las variables del proceso.
* Indicación en pantalla de lazos de control. Capacidad del sistema para trasmitir información (pantalla, informes por impresora, cuadros de alarmas, archivos en soporte electrónico etc.)de la planta.
* Capacidad del sistema para disponer varias pantallas de trabajo tales como: Unidad principal. Sistemas auxiliares, alarmas, históricos etc.
* Capacidades del sistema para la realización de programas de operación automáticos como: Puesta en marcha, puesta en marcha programada, parada, parada de emergencia etc.
– Capacidad del sistema para almacenamiento de valores (datos de planta
y de operación) históricos.
– Capacidad del sistema para realizar cálculos matemáticos tanto simples
como sofisticados y su aplicación al proceso.
Algunos sistemas comerciales de SCD, SCADA o Control distribuido.
UNIDAD DIDÁCTICA 4. OPTIMIZACIÓN DE PROCESOS.
Control avanzado de columnas de destilación, de reactores, de hornos y calderas:
– Conceptos generales. Sistema de control de fondo. Sistema de control de cabeza. Control de presión, Control de calidad. Variables medidas. Variables inferidas. Esquemas usuales de control de destilación.
Control avanzado de mezclas:
– Mezclas.
– Cálculo de propiedades de las mezclas: propiedades lineales y no lineales.
– Control master-ratio. La receta. Propiedades sensibles. Componentes sensibles.
– Control multivariable de mezclas.
La optimización de procesos
– Programación lineal. Optimización no lineal.
– Ordenadores aplicados a la optimización de procesos.
– Ordenadores y SDC.
– Optimización off-line y optimización en tiempo real.
– Las redes neuronales y los sistemas expertos.
Salas de control
– Descripción general de un cuarto de control.
– Entradas y salidas de información.
– Instalación eléctrica. Acondicionamiento del local. Ergonomía (iluminación, trabajo con pantallas de visualización). Comunicación con el exterior. Vigilancia remota.
UNIDAD DIDÁCTICA 1. EL CONTROL “AVANZADO”. DESARROLLOS POSTERIORES AL CONTROL PID.
Variantes del control avanzado.
– Control en cascada. Control anticipativo (feed forward).Control Adaptativo. Control predictivo basado en modelo (MPC). Control óptimo. Control multivariable. DMC (dinamic matriz control).
– Otras estructuras de control: Control por ratio. Control de gama de partida. Control de máximos (override).
UNIDAD DIDÁCTICA 2. CONTROLADORES LÓGICOS PROGRAMABLES (PLC).
Los PLCs: Introducción. Conceptos Básicos. Principios de funcionamiento:
– Representación, convención de símbolos y colores.
– Hardware PLC, Sofware PLC. Principios de lógica y lenguaje de programación.
– Estructura de un PLC: Rack. Bastidor o chasis. Fuente de alimentación. CPU (Sistema operativo y Procesador). Módulos de Entradas (discretas y analógicas). Módulos de Salidas (discretas y analógicas). Memoria. Tiempo de scan.
– Control y programación de procesos utilizando autómatas programables.
* Introducción. Ejemplo ilustrativo.
* Ecuaciones lógicas. Sistemas lógicos combinacionales y secuenciales.
* Aplicación al control de motores. Aplicación a los sistemas de alarma y de seguridad. Aplicación al control de proceso: regeneraciones, arranques, paradas, otras.
UNIDAD DIDÁCTICA 3. SISTEMAS DE CONTROL DIGITAL (SCD, SCADA) EN INDUSTRIA QUÍMICA.
Control Distribuido:
– Definición de Control Distribuido. Descripción general: sistemas analógicos y sistemas digitales.
– Controlador básico (regulador digital). Controlador Multifunción.
– Estación de trabajo del operador.
– Elementos principales: alimentación eléctrica, conexiones de entrada de señal, salidas de señal, módulos e control, módulos de cálculo, registros y
almacenamiento, pantallas de visualización y sistema de operación.
– Secciones y niveles que forman un Control Distribuido.
* Nivel 1 (planta, proceso, sensores, módulos E/S etc.).
* Nivel 2 (control y regulación, controladores, PLCs, PCs etc.).
* Nivel 3 (mando de grupos, PLCs, PCs etc.).
– Nivel 4 (dirección de la producción, estaciones de trabajo, supervisión del
producto, aplicaciones en red).
– Descripción del camino recorrido por la señal de campo (analógica y
digital) hasta la pantalla de trabajo. Indicar con un ejemplo concreto los
elementos por los que circula la señal y los valores que adquiere.
– Descripción del camino recorrido por la señal (orden dada por el operador) desde la pantalla de trabajo hasta el elemento final. Hacer la descripción de forma grafica mediante un ejemplo real.
– Robustez del sistema. Estructuras que la mejoran. Configuraciones del sistema ante el fallo de elementos principales.
– Comunicación del operador con el sistema: El teclado. El ratón. La pantalla táctil.
– Interacción del operador con el sistema. Contenido de las pantallas de trabajo:
* Diagrama de flujo (activo) de la planta en pantalla.
* Indicación en tiempo real de las variables del proceso.
* Indicación en pantalla de lazos de control. Capacidad del sistema para trasmitir información (pantalla, informes por impresora, cuadros de alarmas, archivos en soporte electrónico etc.)de la planta.
* Capacidad del sistema para disponer varias pantallas de trabajo tales como: Unidad principal. Sistemas auxiliares, alarmas, históricos etc.
* Capacidades del sistema para la realización de programas de operación automáticos como: Puesta en marcha, puesta en marcha programada, parada, parada de emergencia etc.
– Capacidad del sistema para almacenamiento de valores (datos de planta
y de operación) históricos.
– Capacidad del sistema para realizar cálculos matemáticos tanto simples
como sofisticados y su aplicación al proceso.
Algunos sistemas comerciales de SCD, SCADA o Control distribuido.
UNIDAD DIDÁCTICA 4. OPTIMIZACIÓN DE PROCESOS.
Control avanzado de columnas de destilación, de reactores, de hornos y calderas:
– Conceptos generales. Sistema de control de fondo. Sistema de control de cabeza. Control de presión, Control de calidad. Variables medidas. Variables inferidas. Esquemas usuales de control de destilación.
Control avanzado de mezclas:
– Mezclas.
– Cálculo de propiedades de las mezclas: propiedades lineales y no lineales.
– Control master-ratio. La receta. Propiedades sensibles. Componentes sensibles.
– Control multivariable de mezclas.
La optimización de procesos
– Programación lineal. Optimización no lineal.
– Ordenadores aplicados a la optimización de procesos.
– Ordenadores y SDC.
– Optimización off-line y optimización en tiempo real.
– Las redes neuronales y los sistemas expertos.
Salas de control
– Descripción general de un cuarto de control.
– Entradas y salidas de información.
– Instalación eléctrica. Acondicionamiento del local. Ergonomía (iluminación, trabajo con pantallas de visualización). Comunicación con el exterior. Vigilancia remota.